Will manuals soon become obsolete with AI?
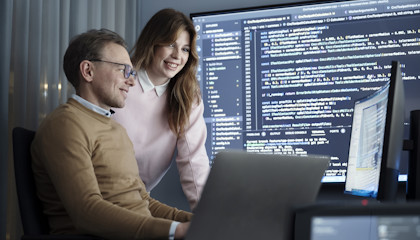
If you said “yes”, you would be correct.
The age of instruction manuals is coming to an end. Who needs them when AI can provide real-time, personalized guidance? Generative AI is the future of learning and application mastery.
Why instruction manuals might come to an end
Roughly one in five (20%) rarely bother to read the instruction manuals after any new purchase. In this context, I refer to manuals in digital and paper format.
According to Deloitte’s Future of Manufacturing report, nearly 20% of a worker's time in industrial settings is spent on manual tasks such as referencing technical documentation, troubleshooting, or following step-by-step instructions.
And a survey commissioned by the Civil Aviation Authority (CAA) proposed that failure to read instructions can prevent consumers from enjoying their new purchases. While this is the consumers' choice, this is a big no-go for engineers in the manufacturing industry.
Engineers must know exactly how every step in the process works from CAD/CAM all the way through to tool management, machining, metrology, and more. Especially, when issues arise in the process that need to be addressed immediately.
But with recent statistics showing that 1 in 5 experienced engineers are retiring by 2026, this can place companies at risk of losing critical technical knowledge.
That's where Generative AI-powered systems come in and introduce themselves to take on the role of digital co-pilots, guiding younger engineers who are less experienced in efficiently handling machinery and other operations faster than previous manuals and even forms of training.
Solution of expertise deficit
One of the biggest challenges to manufacturing is, in fact, the retiring workforce. An aging cadre of engineers, upon retirement, take a great deal of hard-won knowledge with them when they leave.
Another challenge is keeping up to date with capabilities in the evolving software and unleashing capabilities as the shop floor evolves. AI co-pilots are developed to absorb technical manuals and learn system behaviors to offset the long learning curve newer engineers would normally walk into.
These 24/7 available multi-language assistants can then review all sorts of detailed documents, including videos and illustrations, analyze machine data in real time, and put forth solutions based on the decades of accumulated expertise.
For example, in Sandvik, we have developed a Manufacturing Copilot to enable a shift in the user experience with seamless access to knowledge, which is not broadly accessible today, simplifying the user-experience.
A colleague at Sandvik recently shared with me, when he worked as a technical expert in sales, 70% of his responses to salespeople were: ‘open the catalog, page A37, and you'll find exactly what you need.'
This highlights the untapped potential for efficiency— Generative AI transforms how we access and apply critical information, allowing us to focus on innovation instead of routine tasks. By integrating AI as a dynamic partner, industries can adapt to evolving software landscapes:
- Generative AI can analyze new updates and features within industrial software and quickly generate personalized guidance or tutorials to help engineers and operators understand how to use these capabilities effectively. This minimizes the learning curve for new software versions.
- Generative AI can facilitate seamless communication between different software applications and platforms. By creating interfaces and workflows that connect disparate tools (like CAD, CAM, PLM, or metrology software), AI ensures that new features are not only utilized in isolation but also contribute to a cohesive and efficient system.
- AI infused copilots embedded in manufacturing software can provide real-time suggestions, answer queries, and assist in applying new software features within existing workflows. This allows engineers to use new tools effectively without disrupting their regular operations.
The initial phase involves using generative AI to assist in component design by interpreting prompts, enabling contextual queries, and offering suggestions from internal product knowledge – available 24/7 in any language. The next step is the development of the Manufacturing Copilot into an intelligent user experience.
This next phase of intelligent user experience will enable smoother processes that collaborate to optimize and validate processes through integration with their products. In the final phase, the plan includes the option to incorporate voice commands and command-line interfaces for managing manufacturing.
In enabling organizations to keep running smoothly and solve problems before they become disruptions, is the type of predictive capability that leads to huge cost benefits.
A look ahead: The next evolution of AI in manufacturing
The effect of this development is that manufacturing co-pilots will also increasingly begin to handle full processes with very little human oversight. With AI-generated knowledge-based engineering and continuous learning capability, industries will be able to have frictionless transitions as experienced engineers retire and also train the next generation with real-time support and guidance.
Manufacturing in the future will be an innovation-operational efficiency combination, thanks to a powerful mix of human expertise and AI-powered insights.
Similar articles you might be interested in.