Enhancing CNC machining precision and efficiency through advanced software integration
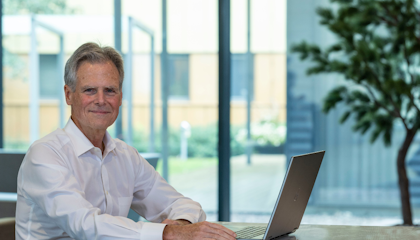
How to stop writing “checks” your CNC machines can’t cash.
When was the last time you wrote a personal check to pay for anything?
Being a 5-axis NC programmer trained in the late 1970’s, I remember when personal checks were how you paid for just about everything.
Handwritten accounting ledgers (checkbooks) were maintained to track account activity and remaining balance. Occasionally, a minor bookkeeping error or miscommunication between accounting partners led to less money being available than the ledgers showed.
Attempting to spend more money than was in the account resulted in overdraft fines, or banks would simply refuse payment and return the offending checks (known as “bounced” checks) because insufficient funds were available. Penalty charges worsened the balance deficit problem, often causing even more checks to bounce which sometimes took a while to recover from.
Later in the 1980’s an amazing technological advancement emerged: computer-based online access to banking accounts. Electronic access (or “connectivity”) made it possible for customers to manage their accounts remotely through computers, their cell phones or other personal data devices.
The evolution of online banking has since become normal and expected in modern banking, reshaping the way customers interact with financial institutions.
Near perfect accounting became effortless and instantaneous, saving time and enabling solid financial decisions to be made based on instant reliable information.
CNC machine connectivity
In the realm of Computer Numerical Control (CNC) machining, we are witnessing a similar technology shift. The ability to connect to CNC controls (the “brainboxes” which drive industrial cutting machines) and software integrations that can make use of these connections is ushering in a new era of precision, efficiency, and informed decision-making regarding machine tool use and machining processes. This blog post explores the pivotal role that software plays in leveraging CNC machine connectivity to achieve previously unattainable levels of toolpath simulation accuracy, optimizing CNC processes, and empowering users with insightful data for improved decision-making in machine utilization. Real-world examples will illustrate tangible benefits provided by software connected to CNC machines, and why this powerful integration is quickly becoming a necessity for machine shops to be at the top of their game.
More accurate toolpath simulation
Toolpath simulation is a virtual representation of cutting tool movement and resultant machining processes. NC programmers rely upon this digital environment to detect potential collisions, identify machine errors, verify correctness of programmed toolpaths, and judge effectiveness of machining strategies.
Think of an NC program as a “check” written by the programmer with the intent of producing a particular machined part. Then the NC machine would be the “bank” where the check will be processed. If no significant issues are encountered, the check is “cashed”, and a successful machined part is the product.
But there are less successful ways this could turn out. “Penalties” can result, such as stock material and machine time wasted creating unusable scrap parts (many programmers have kept a few of these “bounced checks” at their desks - reminders of what NOT to do), damaged or broken cutters, fixtures or machine tools. All these examples cause unexpected expense and downtime to repair or replace them.
Regimented toolpath simulation significantly improves chances for success since potential machining issues can be identified and corrected before actual machining takes place.
Input data quality provides the foundation for robust and trustworthy simulation. Proven foundational strategies include using the most accurate “Digital Twin” representation of the CNC machine that your simulation will support and driving the simulation with the “G-code” (post-processed) version of the toolpath since that’s what will be used on the machine.
Savy simulation users also know that accurate models must be used to represent the various components, e.g. the stock workpiece, fixture hardware, as-designed part, cutting tool assemblies, and components of the machine that are at risk of colliding.
Omitting or scrimping on any of these strategies degrades simulation reliability and may invalidate simulation results.
Toolpath simulation is only as good as the data you feed it.
A great example is when RO-RA Aviation Systems GmbH, an expert in manufacturing complex, high-precision components decided to use CGTech’s Force module, in addition to Vericut to optimize their machining processes.
Did you enter the right data into the control?
This is another side of the story that often occurs in the shop. To run an NC program, someone must setup the stock material and fixture on the machine, load the NC program into the control, ensure the necessary cutting tools are setup and present in the machine, and that the appropriate tool and work/fixture offsets have been entered into the control.
Every time a machine’s Cycle Start button is about to be pressed, especially after a new NC program has been loaded the question becomes, “how closely does the real NC machine environment match what was simulated and verified to be correct?”
In other words, will the NC machine successfully “cash” the NC programmer’s check, or will the check “bounce” due to machining problems yet to be discovered?
If it bounces, how much will that cost? The simple fact is differences between simulated and NC machine environments jeopardize outcomes experienced on the machine.
A common example occurs when a cutting tool, or an offset used in the machine doesn’t match what was in the simulation. Such differences can lead to the tool not cutting the part as expected. Or worse, the NC machine may crash into the part setup causing substantial damage.
Software that leverages CNC machine connectivity provides higher levels of insurance via real-time synchronization between software and CNC controls. Accessing job data that resides in the control (current NC programs loaded, information about cutting tools, tool and work/fixture offsets, and relevant machine parameters) and comparing to what was simulated can identify discrepancies. This provides an opportunity to investigate and resolve differences prior to machining, thereby avoiding “unpleasant” surprises on the machine where the penalty can be quite expensive.
Optimizing and monitoring CNC processes
Optimizing NC programs has become integral for top manufacturing companies to remain competitive and profitable. Optimization software plays a key role taking on the daunting task of calculating optimal feedrates for all types of cutters used to machine a multitude of stock materials.
The most advanced optimization does double duty: increasing program feedrates when cutters are underperforming, and reducing feedrates to avoid overload conditions, so cutters operate consistently within their prescribed performance limits.
But how does one “know” that calculated optimized feedrates were achieved on the CNC machine? And, how well was cutting performed on the machine? As cutters become worn, what (if anything) can be done to maintain cut part quality and prolong cutter life?
Access to data for informed or automated decision-making
Machine monitoring software connected to CNC machines provides visibility and comprehensive information about overall equipment efficiency (OEE).
Detailed insights are provided, often displayed in colorful dashboards to make it easier to monitor machine uptime, downtime, overrides applied, etc.
Analyzing collected data regarding machine downtime, idle times, and tool change frequency allows for informed decision-making to improve machine utilization and machining processes.
Toolpath simulation and optimization software
In conjunction with machine monitoring software raises the bar further to unlock at least three revolutionary capabilities:
- Monitored machine feedrates can be compared to feedrates scheduled in the NC program to determine if the machine achieved them. In cases where feedrates frequently aren’t achieved, investigation can help determine if the machine is capable of reaching the programmed feedrates under present machining conditions, if lower feedrate values may be necessary, or if the job may be better suited run on a different (more powerful) machine tool.
- Monitoring machine performance, such as spindle power or vibration and comparing predictions made by simulation software can provide data-driven insights about the machining process. For example, encountering significantly less spindle power or vibration than predicted could be caused by the machine (or stock material) not being in the correct location, the wrong cutting tool being loaded, or a broken tool. On the other hand, significantly higher than predicted values could result from encountering material where it wasn’t expected which could be due to incorrect stock size, using the wrong cutting tool, missing or incorrect offsets in the control or related conditions.
- Real-time monitoring of machine performance can help to identify machining trends and apply immediate adjustments, such as overriding spindle speeds, feedrates or performing tool changes, based on real-time feedback from the machine. For example, if a piece of stock is slightly thicker, or harder than expected, or a cutting tool is becoming worn, the feedrate can be adjusted slightly slower (via temporary override) enabling machining to continue without interruption. When a trend becomes too pronounced, it may be time to halt the machine and raise a warning describing what triggered the interruption. These types of mitigating actions can help avoid, or at least minimize damage incurred by the NC machine or part when unexpected machining conditions are encountered, or as conditions worsen.
Challenges and future developments
One of the challenges for any novel emerging technology is educating potential adopters about exciting new solutions that are now within reach.
In CNC manufacturing, many companies have become numb to the problems described above and corresponding expenses, so they simply aren’t looking for solutions even when they exist.
Another challenge that comes with connectivity is dealing with cybersecurity concerns. Software integrations that connect to CNC machines must not introduce potential vulnerabilities. Ongoing efforts to enhance cybersecurity measures are essential to safeguard CNC systems from cyber threats.
The future for software integrations with CNC machine connectivity is even brighter and wider reaching than most people have begun to realize.
Following the evolutionary path that was just described (toolpath simulation > optimization/machining prediction > connected machines/real-time monitoring > trend spotting/adjustments > …), the next logical advancement is to apply “machine learning” and develop Artificial Intelligence (AI) algorithms for adaptive and self-optimizing CNC machining processes.
This automation will further enhance machining precision and efficiency through intelligent and data-driven decision-making. While this may sound like a sci-fi movie, much of this is already in various stages of development.
In just a few short years, expect to see NC programmers able to write “checks” (NC programs) faster, and without concerns about their NC machines being able to “cash” them.
NC programs sent to machines will have been simulated, optimized, and expected performance logged. When run on “connected” NC machines, the machining process will be monitored and fine-tuned continuously via AI-assisted auto-adjustment.
If something unexpected occurs or results deviate too far from expected, machining will be halted with notifications sent requesting someone to investigate issues that AI cannot find a way to correct (yet).