How to centralize data for a digital transformation

Learn how shop floors can streamline data into a centralized system and create a unified namespace.
Understanding Industry 3.0 and the rise of digital transformation through data
Since Industry 3.0, the rise of digital transformation has been rapidly shifting with technology. So, what is digital transformation in Industry 4.0 and beyond? It all starts with data.
How can shop floors transform 3.0 data and processes into a more streamlined analysis?
With the rise of automation, the inception of Industry 3.0 marked a significant turning point in manufacturing, introducing automation to streamline processes and enhance productivity.
With the arrival of automation, vast amounts of data began to flow from every corner of the manufacturing process. This data was collected in what is known as the "automation stack" or "automation silo," comprising several layers:
- Shop Floor: The base layer includes Programmable Logic Controllers (PLCs) and sensors, responsible for gathering data from the manufacturing equipment.
- Supervisory Control and Data Acquisition (SCADA): The layer above the shop floor, where data from various sensors and tools are collated and managed.
- MES (Manufacturing Execution System): The layer where machine management, equipment efficiency, machine allocation, and other operational aspects are maintained.
- ERP (Enterprise Resource Planning): One level above MES, this layer handles broader management functions such as inventory, supply chain, and production planning.
- Cloud: Moving all these layers of resources to the cloud platform.
Industry 3.0 successfully brought automation to manufacturing but faced challenges in seamlessly integrating data across different layers. Each transformation of data from one layer to another incurred significant costs, creating an obstacle in optimizing the manufacturing process.
But with the rise of Industry 4.0 and the speed in which technologies evolve – now you can make the shift and move past the roadblocks from 3.0 – which took a significant amount of time to move data from one layer to another.
Manufacturing Industry 4.0: Harnessing the power of data
With Industry 4.0 now you can take your data from every level. Industry 4.0 allows you to centralize this data into a unified namespace. A namespace is a term primarily used in computing, essentially giving all the different types of data a unique identifying name, helping to further a complete analysis of all your shop floor data.
This approach enables us to break free from the constraints of the past and allows direct data consumption from different layers of the manufacturing ecosystem to enable pro-active decision making and understand where to make process improvements.
Understanding how to overcome the barriers to an optimal, fast moving digital transformation is the first step. According to product specialist in digital transformation solutions Matt Smith, you not only need to ensure the right solutions, but it’s just as important that your staff is also onboard and understands the data needed and the why it’s important.
Your team will need to be involved in converting manual and paper-based processes into digital formats, and ensuring data is easily accessible, traceable, and usable. This lays the foundation for seamless data integration.
Key steps to implementing a digital transformation
- Data collection. The first step is to gather data from the shop floor and various automation stack levels. This includes information from sensors, measuring equipment, machine operations, and more.
- Centralization and traceability. The collected data must be centralized into a unified namespace. Additionally, it should be accompanied by traceability information, allowing manufacturers to track the origin and context of each data point.
- Quality management system (QMS) integration. QMS plays a critical role in the digital transformation journey. It ensures that data complies with quality standards and provides the necessary structure for organizing, managing, and analyzing the data.
- Leveraging IoT and Message Queuing Telemetry Transport (MQTT). Industry 4.0 leverages the Internet of Things (IoT) and MQTT protocols to facilitate seamless decision-making information.
What is quality 4.0 and how to achieve it?
Quality 4.0 is part of Industry 4.0, with no direct definition, it’s a trait that involves using digital solutions to help manufacturers improve their processes and more.
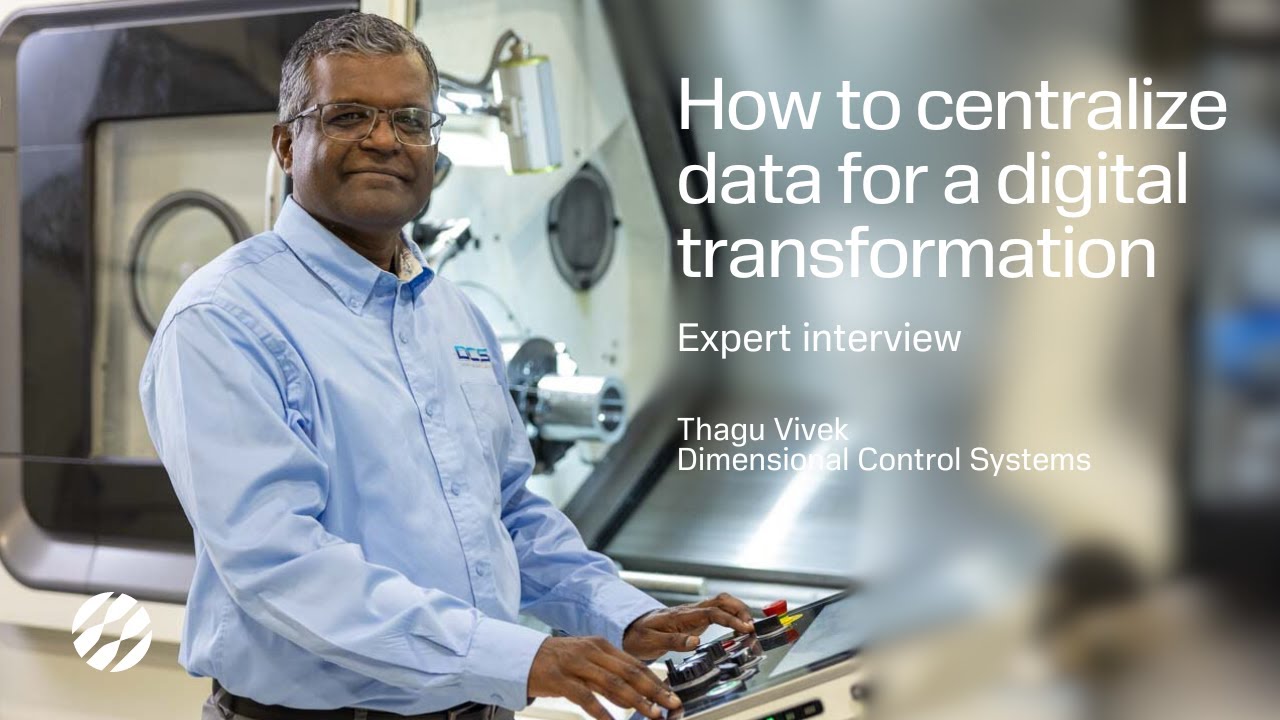
Every company has a current quality footprint and processes in place, although some may need streamlining to improve efficiency and effectiveness. And therefore, look at Quality 4.0 as a journey and not a destination.
You are basically taking your current business processes and evolving them into a digital framework.
Every company is at different stages of their digital transformation in each quality area. You can however categorize the Quality data assets into three categories:
- Paper-based manual collection and storage.
- Manual data collection of quality data and registering them in digital spreadsheets.
- Metrology tools and software registering data in inspection files or local databases.
Usually, companies have a combination of these categories. QMS systems play a critical role in transforming the paper-based systems to digital assets, spreadsheet-entered data, inspection results files, and local database data to a centralized relational database.
As an example, Dimensional Control Systems also known as DCS, offers QDM. In the following link you can see how a quality management system (QMS) plays a pivotal role in the path toward a digital transformation. To begin, start with the system that provides a company-wide user interface to bring all your different types of data into one centralized database.
Once all your different data types are centralized, the solution will apply company quality metrics to create a dashboard and analysis report that can be accessed and distributed across your entire company.
These reports using statistical process control (SPC) tools help you monitor process behavior and allow you and your team to discover issues and find solutions to your production issues. The reporting also includes compliance reports and dashboards.
Now the Quality data framework can continue to leverage the quality information that’s generated by your shop floor systems, IOT devices, and data published, all unified in a namespace thus extending the QMS footprint to Quality 4.0.
As you take the next steps toward your manufacturing digital transformation, you now understand how centralizing data into a unified environment is one of major steps to leverage advanced technologies like IoT, so that manufacturers like yourself can unlock the full potential of Industry 4.0.