Success in sustainable manufacturing for small and medium enterprises
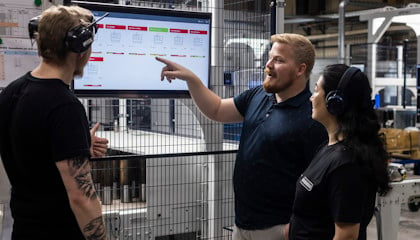
Reducing environmental impacts with digital solutions and partnering with the right suppliers, and training staff, can be achieved. Learn how in this blog.
How to shift into sustainable manufacturing?
Shifting to sustainable manufacturing can be quite overwhelming. To make the shift companies need to break down initiatives into manageable pieces. It’s important to start with achievable tasks and ensure that you understand and focus on the primary contributors to emissions.
A key part to manufacturing is sustainability
In an age of increasing global concern over environmental issues, the manufacturing industry stands at a crossroad. Sustainable manufacturing is no longer a buzzword but a necessity, and its importance in the manufacturing industry cannot be overstated.
In the middle of increasing global alarm surrounding climate change, resource depletion and environmental pollution, the manufacturing sector is significantly impacted. The choices we make today will determine the impact on companies and global health of tomorrow.
While some may view the manufacturing industry as a part of the problem, it’s also increasingly being recognized as a key part of the solution. By re-engineering operations and processes - businesses who embrace sustainable technologies and innovations can become pioneers of change.
This blog post explores what sustainability manufacturing means with real-world examples from our Lighthouse partner Fårbo Mekaniska. Discover the why and how Fårbo initiated their journey towards becoming a more sustainable company now and for the future.
However, before diving into Fårbo’s journey let’s review some key goals the company set out:
- Implementation of initiatives and processes to minimize waste, optimize energy use, and reduce raw material consumption.
- Adaptation of the company to use of renewable energy sources to drastically reduces greenhouse gas emissions.
- Recycling of resources, components, and materials to aim for a closed loop system to minimize waste.
- Collaboration with suppliers to prioritize eco-friendly practices and ethical local sourcing.
- Prioritizing employee health and safety fosters a company culture that attracts socially responsible workers that contributes to long-term business sustainability.
On top of facilitating this shift there are several important standards, initiatives and regulations that have been established in the realm of sustainability.
As of today, larger enterprises are paying close attention to these initiatives and regulations, while small to medium (SME) sized companies in the manufacturing industry have a mixed understanding.
Three important examples of sustainable initiatives and regulations to understand
Corporate Sustainability Reporting Directive (CSRD), a European Union initiative aimed at enhancing corporate transparency and accountability regarding sustainability matters.
CSRD introduces mandatory sustainability initiatives with reporting, ensuring consistent and comparable information. The directive emphasizes the integration of environmental, social, and governance factors into business strategies, promoting sustainable practices across industries.
Science based Target (SBTi), a global initiative that provides a standardized framework for companies to assess and validate their emissions reduction goals, in line with the Paris Agreement goals. Adhering to SBTi enhances sustainability efforts and is voluntary for companies.
Definition of Carbon emission, according to the leading Green House Gas (GHG) a standard corporate protocol, a company's greenhouse gas emissions are classified into three scopes, scope 1, 2 and 3.
- Scope 1 is direct emission from company's own operations.
- Scope 2 are emissions from the energy (electricity, heating and cooling) that the company consumes
- Scope3 is classified as indirect emission from company's upstream and downstream processes that occur outside of their own operations.
As the graphic below illustrates, a subcontractor in the manufacturing industry their main emissions are identified in the upstream processes like material suppliers.
Fårbo’s journey to sustainability
Now, let’s peek inside how Fårbo Mekaniska started their sustainability journey. The following will explore their approach, challenges and opportunities.
Quick facts about Fårbo Mekaniska
- Contract manufacturing company located in Fagersta, Sweden.
- 35 years of experience in the manufacturing industry.
- Specialize in CNC turning, milling, and EDM manufacturing.
- Long series production and small batch production.
- In the middle of a digital transformation and growth journey.
When did Fårbo’s manufacturing sustainability initiative take off?
In 2021, the sustainability topic was brought up for the first time during a board meeting, and simultaneously Mikael Vetterskog assumed the roles as both partner and CEO within Fårbo Mekaniska.
The board concluded that the sustainability topic will be one of several important topics in their company’s strategy.
As a coincidence, just a few months later, Fårbo participated in a bid for a significant potential order. The request included stringent criteria, particularly focusing on their approach to monitoring:
- CO2 emissions,
- Strategies for minimizing their environmental impact, and
- Plans to further reduce their CO2 footprint
This request marked the beginning of Fåbro adopting a more structured approach to sustainability efforts.
How and where to steer your company towards a more sustainable direction may seem broad and occasionally overwhelming. But breaking it down into manageable pieces is what enabled Vetterskog and the Fårbo team to succeed. With these manageable pieces, the team comprehended and concentrated on the primary contributors to their emissions.
Here’s where Fårbo started their sustainability journey
Heating system
One major step taken was the replacement of their heating system. It became evident, relatively quickly, that the existing system was a major source of CO2 emissions and the fact that the system had been in use for several years made the decision to replace it quite straightforward.
Consequently, the old oil-based heating system was substituted with a carbon-neutral alternative—geothermal heating and a district heating system. This change resulted in a reduction of CO2 emission by 40 tons per year, demonstrating a significant positive effect.
Material and tool usage
Sorting and recycling of material chips, as well as the recycling of worn-out cutters and inserts, was already an established process, which has been further refined and stabilized. Today 100% of removed materials and all worn-out tools are recycled and sold back to the suppliers.
Company vehicles
All company cars have been replaced with pure electric vehicles, to further reduce their emissions.
Digitalization
Further refining their sustainability initiatives, Fårbo initiated a digital transformation project with the goal of improving their preparation and production processes to reduce waste to gain more efficient use of assets and equipment.
To accomplish this, Fårbo did so by establishing a complete virtual CAM process using GibbsCAM for part programming and CGTech’s simulation solution Vericut to virtually validate the complete machining processes. This enabled Fårbo to get machined parts right the first time - reducing the number of scrapped parts and consequently using less material per order.
Through their optimization of machine usage, Fårbo anticipated a more efficient utilization of energy consumed by the machines. Vetterskog shared this initiative will help them to achieve a 5-10% reduction in machine energy consumption. (left) Fredrik Svensson, Business Development Manager, Sandvik’s Lighthouse program (right) Mikael Vetterskog, CEO, Fårbo Mekaniska AB.
“It is quite easy to identify the first initiatives and act on them as single one-shot activities but, what requires more effort is cultivating a culture and building a structured way of working within our company where sustainable manufacturing becomes a natural part of our daily behaviors,” Vetterskog said. “For us it was very clear after the first time we were exposed to a customer requirement about our sustainability efforts, that this is something we need to adapt to and make sure over time it becomes a natural part of our operations and strategy going forward.”
For us it was very clear after the first time we were exposed to a customer requirement about our sustainability efforts, that this is something we need to adapt to make sure over time it becomes a natural part of our operations and strategy going forward.
Fårbo going forward
Vetterskog emphasizes their sustainability efforts must rely on accurate and reliable data, enabling them to make systematic and fact-based decisions moving forward.
“Our next important step is to gain control of the sustainability-related data. We are working to establish the foundation for a systematic and automated approach, allowing us to move away from manual, time-consuming work to enhance the accuracy of our sustainability efforts,” said Vetterskog.
Over the past year, the Fårbo team explored several solutions for structuring and managing their data. After careful consideration, they decided to utilize a newly released module in their ERP system, Monitor, known as "Sustainability by Monitor." This module serves as the cornerstone for managing all sustainability-related data.
Vetterskog added, they will secure data sheets for every material from their suppliers, enabling them to make more active and informed choices in selecting both materials and suppliers.
One major initiative will be to look at scope 3 for the transportation chain and evaluate to comprehend their full carbon footprint and identify opportunities for improvement. Supplier selection will be more localized and carefully done.
Looking further ahead, Vetterskog shared it will be crucial to monitor and control the energy consumption of their machines and assets.
With data on each machine/machine group, he said, “they can make more informed, data-driven decisions to improve efficiency and usage of their assets, to further reduce energy consumption.”
Currently, Fårbo has not yet set a target to become CO2 Net Zero, but it is a topic in their ongoing strategy discussion.
Fårbo challenges
Vetterskog emphasized shifting to integrate a sustainable manufacturing approach into the company has been a time-consuming and a complicated process, and they are just at the beginning of the transformation.
Sharing, first, they needed to learn and understand what sustainability regulations and standards to follow. This required genuine interest and a true believing that this is the right path forward for their company.
They see this as a journey involving more and more people in their sustainability work. They believed in taking a stepwise approach to get all their employees to embrace the change in mindset, building a company culture where environmental and long-term sustainability topics are a natural part of every employee's daily work.
Initially, all emission data was collected manually to identify areas for action. The team soon realized the manual approach was not scalable; it was too time-consuming and less accurate. Integration into their daily processes will be essential for success and will take time and patience from their staff.
The team soon realized the manual approach was not scalable; it was too time-consuming and less accurate.
Collecting quality data from suppliers was a tough challenge initially and remains a somewhat time-consuming task for Fårbo. This area will be an ongoing focus for their improvements.
Opportunities (Not just a tick in a box)
Fårbo strongly believes that their sustainability effort is a natural and strategic part of building a future proof company and long-term business. Vetterskog added, “it’s not only a tick in the box and then we are done! We believe the ones that do not take this seriously will have challenges to survive in the future.”
By adopting sustainable manufacturing, it’s easy to see them differentiating themselves in the market.
They already have proof that their effort has paid off, and when winning a large contract where their way of working with sustainability and being able to report a CO2 footprint, set them aside from competition. This was the moment of truth.
“Many competitors were disqualified due to not meeting the sustainability requirement in the inquiry,” said Vetterskog.
The trend of inquiries with sustainability requirements is growing, particularly from larger companies.
In the near future, having a CO2 footprint on quotes will become a standard requirement requested by most customers. And quotes lacking a CO2 footprint will likely be discarded.
Their sustainability initiatives will also contribute to an increased employee engagement over time. They believe that many employees, especially from younger generations, are more likely to be motivated and committed to companies demonstrating a dedication to social and environmental responsibility.
Continuing to implement initiatives aligned with their company's values and strategy, while transparently communicating their sustainability efforts helps them to build trust with customers, employees, and partners.
“It’s more than a responsibility—it's an opportunity to future-proof our business and make a positive contribution to the planet,” Vetterskog said.
Ticket to play and stay competitive with sustainable manufacturing
Sustainable manufacturing is happening now. Our environmental situation, regulations, and initiatives are putting pressure on companies today. Large corporations and industry leaders are paving the way and if you want to play, you can’t be sitting on the sidelines.
The manufacturing industry has a responsibility to contribute to solving environmental challenges.
Leveraging skills and competencies will help initiate transformative changes to adopt more sustainable ways of working. As Vetterskog shared, starting small is key; integrate sustainability into your culture and make it a fundamental part of your company's strategy.
Expect challenges; changes take time, and this is a long-term journey, make sure to work with accurate data for well-informed decision-making.
Fårbo Mekaniska's journey exemplifies that sustainability is more than a duty; it's an opportunity for growth. It's a chance for businesses to shape a positive future and make a real impact on the planet.
Sustainable manufacturing is not just an option or a must; it's a ticket to play!